If there’s one word that could be used to describe 2020, it’s “disruption.” From the COVID-19 pandemic to a record-setting hurricane season to devastating wildfires, everything from personal travel plans to manufacturing supply chains has been disrupted.
Although everyone hopes that the upheaval that has marked 2020 will subside as we move into 2021, it’s important that businesses don’t forget the valuable lessons they have learned this year, and apply them to future operations and planning. By implementing these lessons, your business can avoid many of the slowdowns and other disruptions you experienced this year in the future.
Therefore, as you make your plans for next year and beyond, keep these five key tips and lessons in mind.
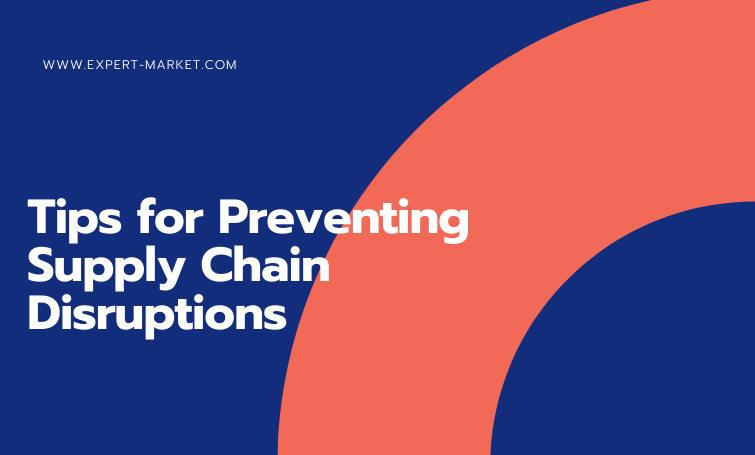
1. Maintain Constant Insight Into Your Supply Chain
How much do you know about your supply chain? Do you have complete insight into each of your supplier’s strengths, vulnerabilities, sustainability, and resilience? Do you have the information you need to anticipate potential disruptions and take action before your business is affected?
If you cannot answer “yes” to these questions, then you need to work on building visibility into your supply chain. When you have that visibility, you are not only better positioned to respond to problems before they occur and affect the rest of the chain, but you can build stronger relationships at every level. Knowing where your suppliers stand allows you to develop stronger contracts, and incentivize them for both performance and their resilience in the face of setbacks.
2. Invest in a Third Party Risk Management Solution
One powerful tool for gaining better insight into your suppliers and protecting your supply chain is a third party risk management solution. Using AI-driven technology allows you to better identify threats to your supply chain and take action before a disruption occurs. Beyond that, risk management tools can evaluate suppliers on a range of factors, from public sentiment and news stories to geopolitical factors and cyber threats. Risk management tools identify risks that may have otherwise been hidden, potential bottlenecks and dependencies that can affect your business, and support better decision making and planning.
3. Conduct a Supply Chain Audit
Another aspect of risk management is conducting regular supply chain audits. Performing a thorough risk analysis to identify vulnerabilities and areas where you may need to seek alternatives. This involves looking both at the company itself, but the external factors that could affect their position in the supply chain, such as social or political factors. For example, will political protests block transportation routes, keeping important materials from reaching the manufacturing plant? Does the supplier routinely face shutdowns due to extreme weather? Look for these trends and have a plan to address them when needed.
4. Maintain Backup Plans
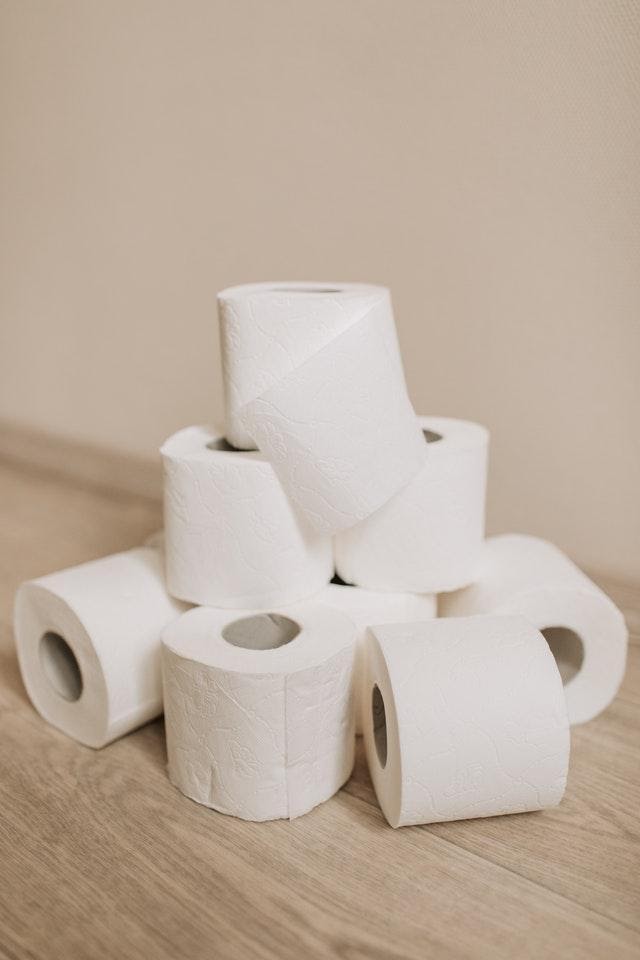
When a supply chain disruption occurs — or demand exceeds your existing supply — and your existing stores of raw materials or finished products is depleted, the results can be devastating to your business.
For example, in the early days of the COVID-19 pandemic, toilet paper was in short supply due to high demand and a shortage of raw materials to make more. Although toilet paper has returned to store shelves, disinfectant wipes have not been as quick to return. One manufacturer, Seventh Generation, notes that this is in part because of supply chain disruptions.The same materials that are used for disinfecting wipes and other hygiene items are used in the manufacture of personal protective equipment, and competition for those materials led to disruptions in their ability to meet demand.
Although it can be difficult to predict events like COVID-19 and the “panic buying” that occurred in the early days of the pandemic, the experience of companies like Seventh Generation, Clorox, and Lysol are a stark reminder that companies need to maintain solid backup plans and inventory to meet these unexpected disruptions. Ideally, your business should be prepared to manage several months of disruption, during which time you can identify alternative suppliers.
5. Have an Emergency Plan
There’s no reason to be caught unaware when supply chain disruptions occur. As you identify vulnerabilities in your supply chain, also identify backup suppliers and diversify your supply base. Your company needs to be proactive to effectively manage emergencies. This includes running stress tests to make adjustments as needed, and identifying areas where your supply chain is weakest.
Remember that any chain is only as strong as its weakest link, so finding it now and taking action to strengthen it will ensure that your company can weather any storm and continue to operate in even the most challenging circumstances.